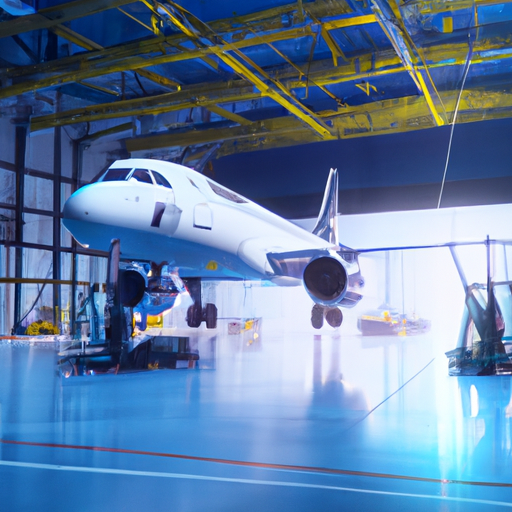
Benefits of Airbus’ New Automated A321XLR Equipping Hangar in Hamburg, Germany
Airbus, the renowned aircraft manufacturer, has recently unveiled its new automated A321XLR equipping hangar in Hamburg, Germany. This state-of-the-art facility is set to revolutionize the aircraft production process and bring numerous benefits to both Airbus and its customers.
One of the key advantages of this new hangar is its ability to significantly increase production efficiency. With the integration of advanced automation technologies, Airbus can streamline the equipping process, reducing the time required to assemble and outfit the A321XLR aircraft. This means that Airbus can produce more planes in a shorter period, meeting the growing demand for air travel worldwide.
Moreover, the automated hangar allows for greater precision and accuracy in the assembly process. By utilizing cutting-edge robotics and artificial intelligence, Airbus can ensure that each component is installed with utmost precision, minimizing the risk of errors or defects. This not only enhances the overall quality of the aircraft but also reduces the need for rework or repairs, saving both time and resources.
Another significant benefit of the new hangar is its positive impact on the environment. Airbus has long been committed to sustainability, and this automated facility aligns perfectly with their goals. By optimizing the production process, the hangar reduces energy consumption and waste generation. Additionally, the use of automation reduces the need for manual labor, minimizing the carbon footprint associated with human activities. This eco-friendly approach is crucial in today’s world, where environmental concerns are at the forefront of many industries.
Furthermore, the automated hangar enhances worker safety and well-being. By automating repetitive and physically demanding tasks, Airbus can reduce the risk of accidents and injuries. This not only protects the employees but also improves their overall job satisfaction. With the implementation of automation, workers can focus on more complex and intellectually stimulating tasks, fostering a more engaging and fulfilling work environment.
In addition to these benefits, the new hangar also offers increased flexibility in aircraft customization. With the use of advanced robotics and digital technologies, Airbus can easily adapt the production process to accommodate various customer preferences and requirements. This means that airlines can have greater control over the design and configuration of their A321XLR aircraft, allowing for a more personalized and tailored flying experience for passengers.
Lastly, the automated hangar in Hamburg strengthens Airbus’ position as a global leader in the aviation industry. By investing in cutting-edge technology and innovation, Airbus demonstrates its commitment to staying ahead of the competition. This state-of-the-art facility showcases Airbus’ dedication to delivering high-quality, efficient, and sustainable aircraft to its customers worldwide.
In conclusion, the unveiling of Airbus’ new automated A321XLR equipping hangar in Hamburg, Germany brings numerous benefits to the aircraft manufacturer and its customers. From increased production efficiency and precision to environmental sustainability and worker safety, this state-of-the-art facility sets a new standard in aircraft production. With its ability to customize aircraft and strengthen Airbus’ global position, the automated hangar is a testament to the company’s commitment to excellence and innovation.
How the Automated A321XLR Equipping Hangar Enhances Efficiency in Aircraft Production
Airbus, the renowned aircraft manufacturer, has recently unveiled its new automated A321XLR equipping hangar in Hamburg, Germany. This state-of-the-art facility is set to revolutionize the way aircraft are produced, enhancing efficiency and streamlining the manufacturing process.
One of the key advantages of the automated A321XLR equipping hangar is its ability to significantly reduce production time. With advanced robotics and automation systems, the hangar can complete tasks that would traditionally take days or even weeks in a matter of hours. This not only speeds up the production process but also allows for a higher volume of aircraft to be manufactured within a given timeframe.
Furthermore, the automated hangar ensures a higher level of precision and accuracy in the assembly of aircraft components. The use of robotics eliminates the risk of human error, resulting in a more consistent and reliable end product. This is particularly crucial in the aviation industry, where safety is of utmost importance. By minimizing the potential for mistakes, the automated hangar contributes to the overall quality and reliability of Airbus aircraft.
In addition to improving efficiency and accuracy, the automated A321XLR equipping hangar also offers a more ergonomic working environment for employees. With the heavy lifting and repetitive tasks being handled by robots, workers can focus on more complex and intellectually stimulating aspects of the production process. This not only enhances job satisfaction but also reduces the risk of physical strain or injuries associated with manual labor.
The hangar’s automation systems are designed to seamlessly integrate with Airbus’ existing production processes. This ensures a smooth transition and allows for the efficient utilization of resources. By optimizing the workflow and minimizing downtime, the automated hangar maximizes productivity and minimizes costs.
Moreover, the automated A321XLR equipping hangar is equipped with advanced data analytics capabilities. This allows for real-time monitoring and analysis of production data, enabling proactive maintenance and predictive troubleshooting. By identifying potential issues before they escalate, Airbus can minimize disruptions and optimize the overall efficiency of the manufacturing process.
The introduction of the automated hangar also aligns with Airbus’ commitment to sustainability. By reducing energy consumption and waste, the hangar contributes to the company’s efforts to minimize its environmental footprint. Additionally, the use of automation reduces the need for manual labor, which can help address labor shortages and create a more sustainable workforce.
In conclusion, the unveiling of Airbus’ new automated A321XLR equipping hangar in Hamburg, Germany marks a significant milestone in aircraft production. This cutting-edge facility enhances efficiency, accuracy, and ergonomics, while also incorporating advanced data analytics capabilities. By streamlining the manufacturing process, Airbus is able to produce a higher volume of aircraft within a shorter timeframe, without compromising on quality or safety. The automated hangar not only revolutionizes the way aircraft are produced but also contributes to Airbus’ commitment to sustainability. With this innovative facility, Airbus continues to lead the way in the aviation industry, setting new standards for efficiency and excellence.
The Impact of Airbus’ New Automated Hangar on the Aviation Industry
Airbus, the renowned aircraft manufacturer, has recently unveiled its new automated A321XLR equipping hangar in Hamburg, Germany. This state-of-the-art facility is set to revolutionize the aviation industry, bringing about significant changes and advancements in aircraft production and maintenance. The impact of this new hangar is far-reaching, affecting various aspects of the aviation industry, from increased efficiency to improved safety measures.
One of the most notable impacts of Airbus’ new automated hangar is the increased efficiency it brings to the aircraft production process. With advanced robotics and automation systems, the hangar streamlines the assembly and equipping of the A321XLR, reducing the time required for these tasks. This means that Airbus can produce more aircraft in a shorter period, meeting the growing demand for air travel worldwide. The increased efficiency also translates into cost savings, as the automated processes minimize the need for manual labor and reduce the risk of errors.
Moreover, the new hangar’s automation systems contribute to improved safety measures in aircraft production. By minimizing human intervention in critical tasks, the risk of accidents and errors is significantly reduced. The advanced robotics and artificial intelligence systems ensure precise and accurate assembly, minimizing the chances of faulty components or systems. This enhanced safety not only benefits the passengers but also the airline companies and Airbus itself, as it reduces the likelihood of costly recalls or maintenance issues.
In addition to the production process, the new hangar also has a significant impact on aircraft maintenance. With its advanced technology and automation systems, the hangar enables faster and more efficient maintenance procedures. The automated equipment can quickly diagnose and address issues, reducing the time an aircraft spends on the ground for repairs. This means that airlines can maximize their fleet’s availability, minimizing disruptions to their schedules and improving customer satisfaction. The improved maintenance procedures also contribute to enhanced safety, as potential issues can be identified and resolved promptly.
Furthermore, Airbus’ new hangar sets a precedent for the aviation industry, showcasing the potential of automation and robotics in aircraft production and maintenance. As other manufacturers and airlines witness the benefits of this technology, they are likely to follow suit, investing in their own automated facilities. This shift towards automation has the potential to transform the industry, making aircraft production and maintenance more efficient, cost-effective, and safe.
However, it is important to note that while automation brings numerous benefits, it also raises concerns about job displacement. As more tasks become automated, there is a possibility of job losses in certain areas of the aviation industry. It is crucial for manufacturers and airlines to address this issue by providing retraining opportunities and creating new roles that complement the automated systems. By doing so, they can ensure a smooth transition and minimize the negative impact on the workforce.
In conclusion, Airbus’ new automated A321XLR equipping hangar in Hamburg, Germany, has a significant impact on the aviation industry. The increased efficiency, improved safety measures, and enhanced maintenance procedures brought about by this state-of-the-art facility are set to revolutionize aircraft production and maintenance. As other manufacturers and airlines take note of these advancements, the industry is likely to witness a shift towards automation, transforming the way aircraft are built and maintained. While there are concerns about job displacement, proactive measures can be taken to mitigate these effects. Overall, Airbus’ new hangar marks a milestone in the aviation industry, paving the way for a more efficient, cost-effective, and safe future.